While both shot blasting and shot peening machines utilize the projection of steel shot media against a metallic part’s surface at high speeds, shot blasting and shot peening machines achieve very different results and are used for entirely different purposes. While Blast-Abrade is known across the country for our sales and service of Goff shot blasting machines, we also sell and service shot peening machines and want to help our website visitors to understand the difference in these two essential industrial operations for treating metal surfaces.
What Is Shot Blasting?
If shot blasting has an aggressive sounding name, it’s because it’s an aggressive process. Shot blasting is a mechanical cleaning process that uses small steel BBs (shot blasting media, pictured below - left) to remove oxides and debris from the surface of metals. The process uses centrifugal force generated in a shot blast machine to hurl or throw the blasting media at the metal surface; the impact acts to strip the metal surface of its impurities, rust, paint and foreign matter. If you’re familiar with the process of sand blasting, you’re on the right track towards understanding shot blasting, although shot blasting is a much more powerful version of sand blasting.
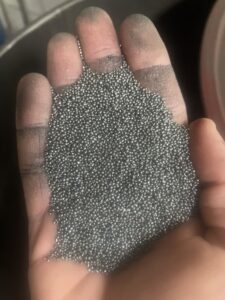
Shot-blast media for use with shot blasting machines
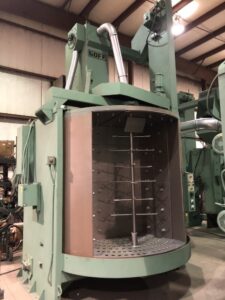
A spinner-hanger shot blast machine ready for action
Shot blasting is used for the mass-cleaning of parts in foundries, forging shops, heat treatment facilities, OEM factories and more. Shot blasting machines such as the Goff shot blaster (seen above – right) blast away surface rust or contaminants, preparing the part for the next step of production. Watch an informative video on the shot blasting process.
What Is Shot Peening?
Shot peening is an engineered blasting operation designed to propel industrial steel-shot media against the surface of steel parts to increase material strength and to reduce failure of critical parts under duress, such as the valve springs in cars or the landing gear in aircraft. “Peening” is a Scandinavian term meaning “to beat-out,” and metalworkers in the past used ball-peen hammers to condition their metal work to make it stronger. Today, with shot peening machines, thousands of tiny ball-peen hammers in the form of shot-peening media barrage and hammer the surface of metal parts within minutes, to render the metal stronger and able to resist surface stress cracking. Shot peening machines add remarkable speed and consistency to this process that once took days to complete - either reducing the amount of time necessary for the peening operation or enabling many more metal elements to be treated by shot peening machines during a standard work shift.
Shot peening is a cold-work method that involves pelting the surface of a metal part with round metallic shots that hit at high velocity. Within shot peening machines, each shot acts as a tiny “peen-hammer” that dents or dimples the metal’s surface and stretches it radially as it hits. The shot’s impact causes a flow in surface fibers that extends below the surface to the depth of impact - typically between .005 to .030". Fibers beneath the top layer retain their elasticity. As a result, the shot-peened surface stays resilient and resists cracking when strained by heavy loads. Almen strips, (pictured below – left) are attached to the metal surface being shot-peened. These special metallic strips register or record the impact of the shot media so that the depth of the impact and the saturation coverage on the metallic surface can be monitored and ensured for accuracy and full coverage.
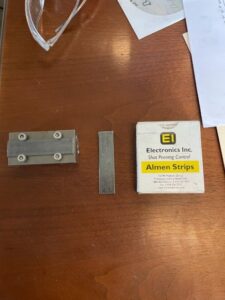
Almen strips are essential when using shot peening machines - they register the depth and saturation of peening on a metal surface.
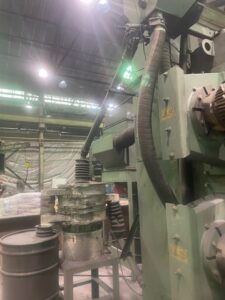
A shot peening machine at work form Blast-Abrade
Shot Peening Machines
Various pieces of shot peening equipment help to facilitate the shot peening process. Shot peening is done with the help of a centrifugal wheel or compressed air-blast nozzle, both of which propel the shot at a desired speed within shot peening machines. The wheel should have a concentrated, efficient blast pattern to keep the cost of the peening media in-check, and blast patterns can be adjusted on shot peening machines. Triple-deck screening classifiers, (one is pictured above – right) are also an important part of the process with shot peening machines, as they continuously remove broken or undersized shot media from the shot peening machine and ensures that a high percentage of full-sized shots remain in the machine. When a shot does eventually break down and becomes too small to impact the metal’s surface and dimple it, a shot-add device instantaneously replaces it with a new shot.
Fatigue Resistance is a Great Benefit of Shot Peening for Metal Surfaces
Shot peening machines are used mostly for ferrous metals, such as steel, and on non-ferrous metals such as bronze, aluminum and titanium. One of shot peening’s most marked benefits is its ability to increase the resistance and durability of parts, especially those inclined to bend or twist. From rocker arms and bearings, to crankshafts and turbine wheels, shot peening machines can extend the life of any part that has a tendency to bend or twist under stress!
With the help of shot peening machines and equipment, a part’s life can lengthen by 30 percent on the low end and up to 1500 percent on the high end (Yes, you read that right)! These longer lifespans result from a shot peening machine’s ability to improve a metal’s resistance, especially that of magnesium alloys. At the same time, shot peening machines can eliminate porosity in aluminum die castings and the leaking that goes along with that porosity. Shot peening machines can also increase a metal’s oil retention properties.
By boosting a metal’s fatigue tolerance and resilience, shot peening machines alleviate the compressive stress placed on metals on the surface or immediately below it. Use the chart below to select arc height as it relates to the thickness of parts that need to be shot peened.
Thickness of Part Arc Height
1/16 .012N
1/8 .008A
1/4 .014A
3/8 .018A
1/2 .021A
5/8 .007C
3/4 .008C
7/8 or greater .010C or greater
Shopt Blasting versus Shot Peening Machines
While shot blasting machines rely on abrasive media to efficiently strip and clean a surface in preparation for the next manufacturing step, shot peening machines rely on the plasticity of metal to extend the life of a part.
Shot blast machines blast-away surface contaminants in preparation for the next stage of production; shot peening machines target the most critical areas of parts to improve their strength and resilience.
At Blast Abrade, we’ve been developing excellence in shot blasting AND shot peening operations since 1978. We are dedicated to helping you on your next shot blasting or shot peening project. Learn more about our Rebuild & Repair services and what we can do for your veteran shot peening machines. Please contact us with any questions or to get started with Blast-Abrade. See our current inventory of Goff shot blasters and shot peening machines. Keep us in-mind for your consulting needs and more - we out-blast the competition and offer systems and turn-key services for both shot blasting and shot peening machines for your industrial and manufacturing needs.